Mass Timber Components and Engineered Wood Products
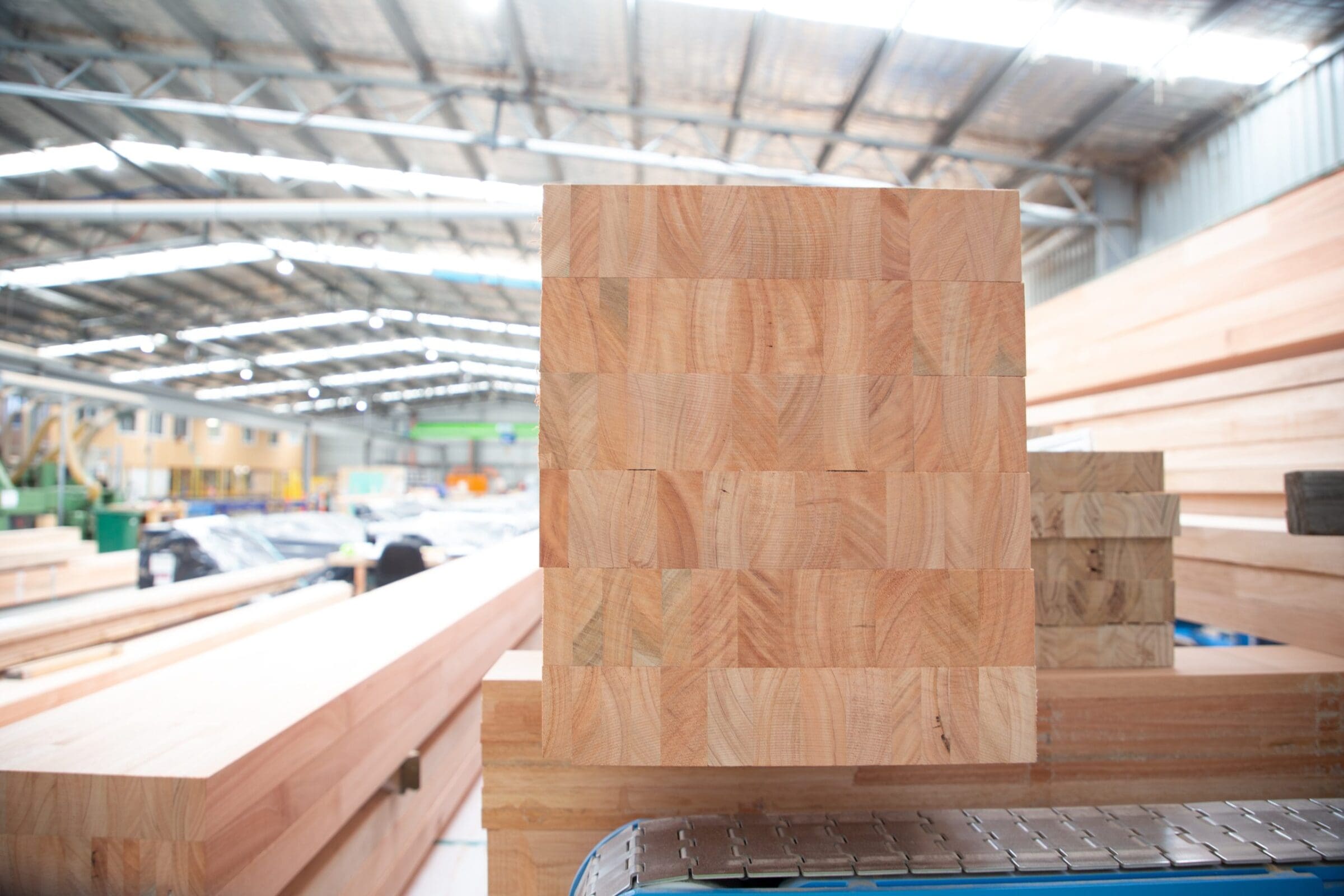
Modern timber products and construction techniques ensure that wood-based solutions can provide effective and efficient alternatives to conventional steel and concrete-based structures for multistorey commercial, public and educational building in Australia’s capital and regional centres.
Largely prefabricated, these timber-rich solutions can be built more quickly than conventional alternatives and generate significantly lower greenhouse gas emissions. Emission-reduction results from the ongoing sequestration of atmospheric carbon stored in the wood and avoiding the emissions associated with the high-energy manufacture of steel and concrete.
Mass timber construction techniques are based on key engineered wood products (EWPs), particularly glue laminated beams (or glulam) and cross laminated timber (CLT), augmented with other EWPs, such as plywood and LVL.
Glue Laminated Beams
Glue laminated timber is sections of sawn timber glued together to form larger, more structurally reliable timber elements. Lamination increases the size, structural capacity and reliability of elements and produces a wide range of beams, columns or panel elements. Curved glulam can also be produced, with the extent of the curve achieved depending on the laminate’s thickness.
While the production process is similar, glulam offers far greater structural reliability than components laminated for joinery. Manufactured for use in building structures, glulam must satisfy strict requirements for glue and structural performance. Very large section sizes are available. Length up to 18 metres are possible but more regularly are available 12 m longs from Tasmanian producers or from interstate producers using Tasmanian species as feedstock.
Cross Laminated Timber
Cross laminated timber (CLT) is engineered wood panels made by joining layers of timber together with the grain direction of alternating layers at right angles, similar to plywood. Most CLT is glue laminated but some is assembled with mechanical fasteners, usually nails.
CLT is usually made for the project as part of an integrated building design, fabrication and delivery process. Different timber grades and thicknesses can be used in the panels, and they can be made to various layer configurations. Panels are usually assembled so that the outside layers run parallel to the direction of span. However, the panels retain substantial bending strength perpendicular to the primary axis due to the inner layers’ spanning capacity.
While Australian produced CLT is manufactured from plantation pine, a Tasmanian producer is making a range of CLT and glulam products from a plantation hardwood feedstock.